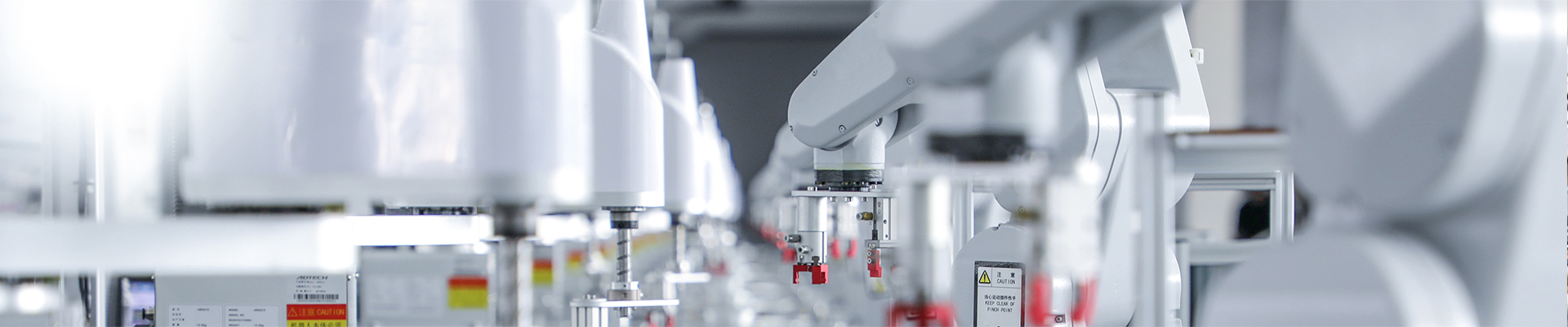
- Home
- >
News
We focus on welding technology and intelligent solutions, provide hardware such as ultra precision welding power supplies and intelligent systems such as welding monitoring and networking group control, and will appear at the 20th Vietnam International Machinery Equipment and Industrial Technology Exhibition in 2024.
Spot welding machines are widely used welding tools, suitable for a variety of non-ferrous metals. The welding quality is affected by parameter adjustment, and attention should be paid to product thickness limitations and equipment maintenance.
The precision spot welding machine has good welding effect. When installing and using it, you need to pay attention to lead selection, safety protection, component tightening and oxide cleaning, ensure the normal voltage of the power grid, and pay attention to the maintenance of wearing parts.
Current detection of precision spot welding machines is the key to ensuring welding quality. Oscilloscope testing may not be accurate, so it is recommended to use a dedicated current tester for monitoring. When purchasing, companies should choose equipment equipped with a current tester and conduct regular testing and calibration to ensure the stability and reliability of welding quality.
Differentiate between DC and AC spot welders: look at welding quality, speed, energy saving effect and equipment size. DC spot welders are high precision, fast, energy-saving and lightweight.
Precision spot welders excel at welding fine components, while seam welders excel at producing continuous welds. The two have different electrode shapes, welding methods, and application areas.
This welding equipment has a high-precision control of 0.2ms and low heat generation to create beautiful and stable solder joints. It integrates current, voltage, power, pressure, and displacement monitoring, and has pre-detection alarm and powerful quality traceability capabilities (recording more than 5 million data). The welding frequency can be flexibly switched between 1-5KHZ to meet various needs.
Automatic feeding nut spot welding machine is accurate and efficient, with firm welding and easy operation. It is a great tool for mass production and can improve both quality and efficiency!