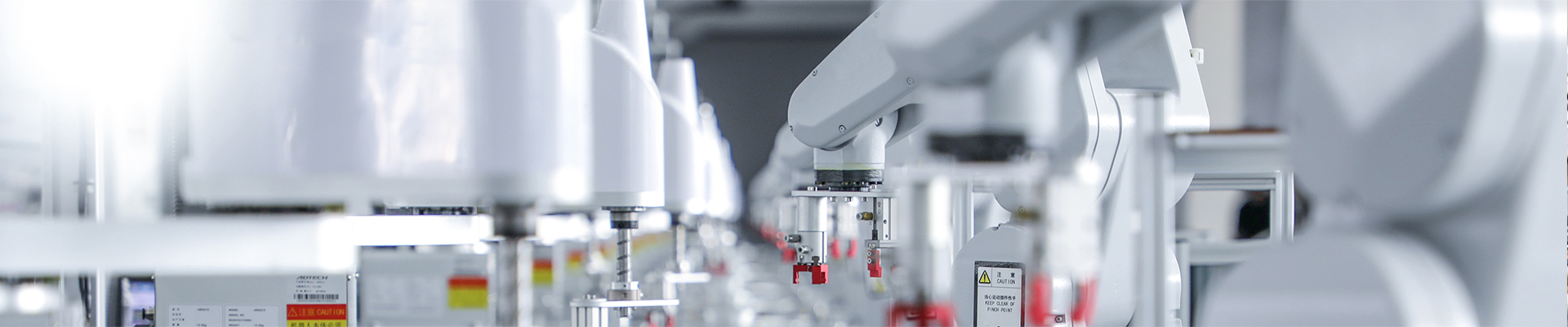
- Home
- >
News
The precision spot welding machine adopts advanced inverter power supply, with stable heat output and fast response; the welding wire does not need to be processed and the operation is efficient; the welding wire diameter range is wide and applicable to many scenarios;
The combination of hanging welding clamp and resistance spot welding machine improves welding accuracy and efficiency. The hanging welding clamp provides a stable operating platform to reduce operator fatigue, while the resistance spot welding machine ensures high-quality welding, which is suitable for high-precision mass production and is widely used in the automotive, electronics and other industries to promote the automation and precision of production lines.
Weld penetration testing methods include metallographic microscope observation, compression test and weld penetration microscope observation. Weld penetration tester measures the temperature change during welding through thermocouples, and the computer analyzes the data to determine the penetration depth. Resistance welding penetration tester helps to optimize welding parameters, monitor the welding process in real time, and ensure welding quality.
When using the copper wire spot welding machine, you need to pay attention to equipment inspection, copper wire selection, safe operation and maintenance to ensure welding quality, operational safety and stable operation of the equipment.
Efficient spiral spring production relies on integrated welding power supply & monitoring for precision welding & quality assurance.
Precision inverter welding equipment has been launched, which improves welding stability and efficiency with a high control accuracy of 0.2 milliseconds. It is widely used in industries such as automobiles, motors, capacitors, solar energy and batteries, promoting industrial upgrading and the development of intelligent manufacturing.
In the field of precision hot-press welding, the selection of welding power source is crucial. AC power source has low cost but low control accuracy and high energy consumption; while inverter power source has complex structure but high control accuracy, fast and stable heating speed and low energy consumption. Therefore, inverter DC welding power source has gradually become the mainstream choice in the field of precision welding and is widely used in many welding fields.