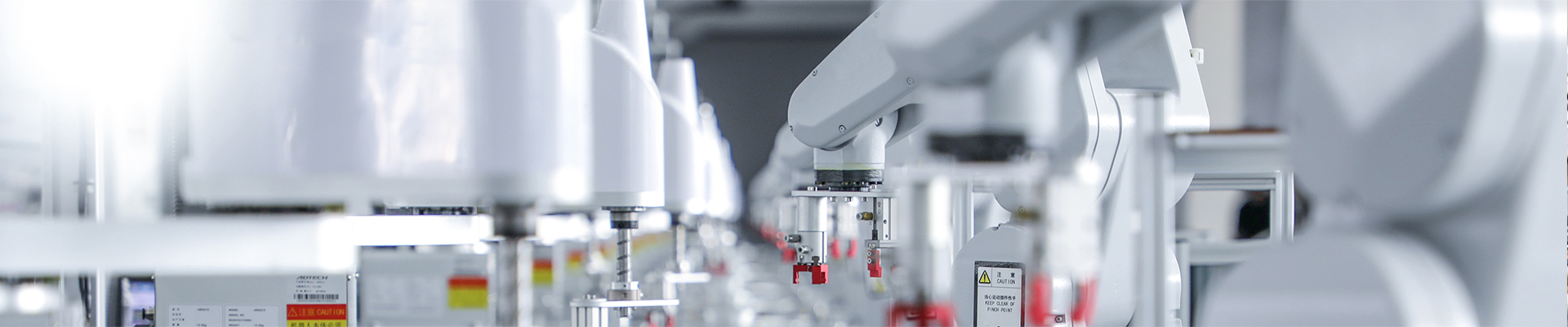
HD-400B welding monitor: a technical benchmark for all-type adaptation and precision monitoring
2025-07-03 10:13In the context of modern intelligent manufacturing and increasingly stringent quality control requirements, real-time monitoring of the welding process is particularly critical. The HD-400B welding monitor launched by Huandian has become an ideal supporting product for various spot welding equipment with its high precision, intelligence and strong compatibility, providing strong support for improving welding quality and process traceability.
The HD-400B welding quality inspection device adopts a high sampling rate digital processing system and has multi-channel real-time monitoring capabilities for key parameters such as current, voltage, power, welding time, pressure, and displacement. HD-400B welding quality inspection device advantage is that HD-400B welding quality inspection device can accurately record the data waveform of each welding, set the upper and lower limit parameter range, and realize automatic judgment and abnormal alarm of welding quality. At the same time, HD-400B welding quality inspection device supports multiple communication methods (such as RS232, RS485, Ethernet), which is convenient for access to the MES system and helps the factory achieve intelligent management.
When used with an AC spot welder, the HD-400B welding real-time monitoring can effectively make up for the shortcomings of traditional AC welding equipment that lack process monitoring. By real-time monitoring of the current waveform, HD-400B welding real-time monitoring can identify welding instability problems caused by power grid fluctuations and improve welding consistency.
For DC inverter spot welders and AC inverter spot welders, the HD-400B welding real-time monitoring can accurately and synchronously capture high-frequency welding signals, provide millisecond-level data accuracy, and help users analyze the forming effects of multiple welding currents and the slow rise and fall process. HD-400B welding real-time monitoring is especially suitable for applications in new energy vehicles, power batteries and other fields with extremely high requirements for welding quality.
When used with a transistor spot welder, the HD-400B transistor spot welding monitor can monitor the response characteristics of each discharge, determine the control effect of the IGBT/transistor switch, and thus determine whether there is poor control or discharge abnormality, which is particularly important for welding of micro-components (such as precision electronics and lead welding).
Combined with an energy storage spot welder, the HD-400B welding traceability system can track the energy changes and waveform consistency of the capacitor discharge process, assist in determining whether the energy storage release is sufficient, and thus ensure the integrity and strength of the weld formation.
In summary, the HD-400B welding traceability system not only has a wide range of adaptability, but also has powerful data diagnosis, quality traceability and abnormal alarm capabilities. HD-400B welding traceability system is an indispensable intelligent terminal for modern welding quality control. Whether spot welding machine is traditional welding process or new intelligent spot welding equipment, the HD-400B welding traceability system can provide accurate and efficient monitoring support, helping users achieve higher quality welding results.